Extrusion melt pump PET production unit finally condensate
This process is a special process. From the second advance polycondensation reactor prepolymer is divided into two road, respectively from the bottom of the disc reactor, at 272 ℃ under the condition of soil 3 ℃, about 130 pa, after about 171 min to complete the final polycondensation reaction, to improve the viscosity of the material by to about 0.682, at the end of the reaction, polymer esterification rate is about 99.8%, the degree of polymerization is about 100.
The finished polymer melt is discharged by the melt discharge pump and is sent by the melt filter to cut the grain.
Normal production, the final polycondensation melt pump in 5 o % load operation, determine the speed of the feed pump according to the production, when production changes can automatically adjust the PTA melt pump, to control the reaction system of material feeding amount.
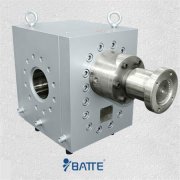
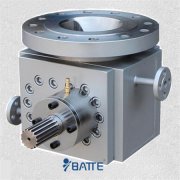
Evaporation during the process of final polycondensation reaction of ethylene glycol vapor from the upper disc reactor, through the scraper condenser, with 28 ℃ glycol liquid spray condensation, spray of ethylene glycol in the circulatory system using 7 ℃ of chilled water for cooling. Two thirds of the fresh ethylene glycol is needed in the reaction system.
By the scraper condenser of non-condensable gas into the ethylene glycol steam ejector, injector is divided into three, all levels of power steam from ethylene glycol evaporator, normal operating temperature is about 202.6 ℃, pressure is 0.098 MPa, all levels of the vacuum degree of up to 100 pa, pa, pa, 3500, 600-1000 from the injector non-condensable gas after vacuum pump system, into the exhaust gas scrubber (the two exhaust gas scrubber can zoomlion, can also be prepared), with industrial water emptying after washing.
Heating jacket of the disc reactor, melt jacketed piping and ethylene glycol evaporator heating coils are by secondary heating liquid heat medium, all the gas phase the jacketed piping and ethylene glycol by gas phase heat medium heating steam injector.
By disc reactor of polymer melt, melt booster pump, after the melt filter, through the melt distribution valve, casts take the lead to take, then fall into underwater pelletizing machine guide plate, with the desalting water spray cooling, the melt in a curing state incised, and further by water cooling and solidification.