Extrusion pump working principle in india
Extrusion pump according to the direction of the head and screw the center line of the angle, the head is divided into bevel head (angle 120o) and right angle head. The head of the shell is bolted to the fuselage, the nose of the mold with a mold core to sit and nut fixed to the nose into the port, the front of the mold core with a mold core, mold core and core seat The center of the hole, for through the core line; in front of the nose are equipped with pressure ring, for equalization pressure; extrusion molding part by the die sets and die sets, the die sleeve position by the bolt through the support to adjust , In order to adjust the relative position of the mold sleeve to the mold core to facilitate the adjustment of the uniformity of the thickness of the extrusion coating. The nose is equipped with heating device and temperature measuring device.
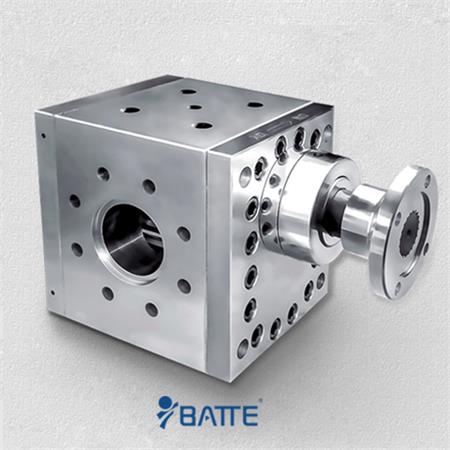
1. Drive system The role of the drive system is to drive the screw, screw the torque and speed required in the extrusion process, usually by the motor, reducer and bearings and other components.
2. Heating and cooling devices Heating and cooling are the necessary conditions for the plastic extrusion process to be carried out.
(1) The extruder pump is usually used for electric heating, divided into resistance heating and induction heating, heating film installed in the fuselage, neck, head of the various parts. Heating device by the external heating tube plastic, so that the temperature, in order to achieve the required temperature of the process operation.
(2) The cooling device is set to ensure that the plastic is in the temperature range required by the process. Specifically, in order to exclude excess heat generated by the shear friction of screw rotation, to avoid the temperature is too high to break down the plastic, scorching or setting difficult. Cylinder cooling is divided into two kinds of water-cooled and air-cooled, the general small and medium-sized extruder with air-cooled more appropriate, large are more water-cooled or combined with the two forms of cooling; screw cooling is mainly used in the center of water-cooled, the purpose is to increase the solid material delivery rate , And stabilize the amount of plastic, while improving product quality; but in the hopper cooling, one is to strengthen the role of solid material transport to prevent the plastic particles due to temperature rise blockage mouth, and second, to ensure that the transmission part of the normal work.